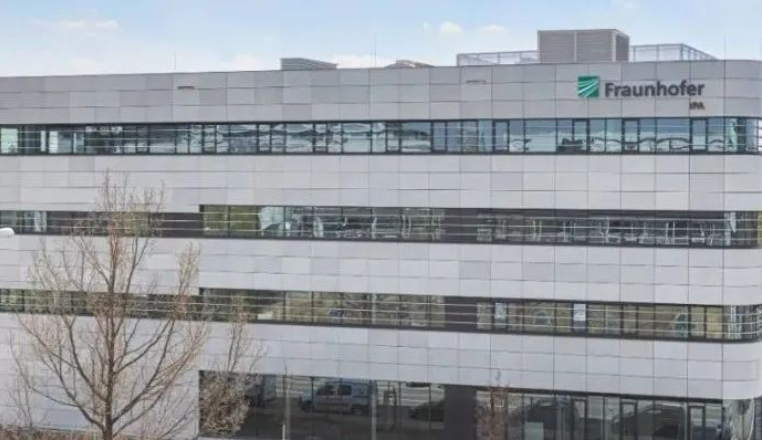
© Fraunhofer IPA
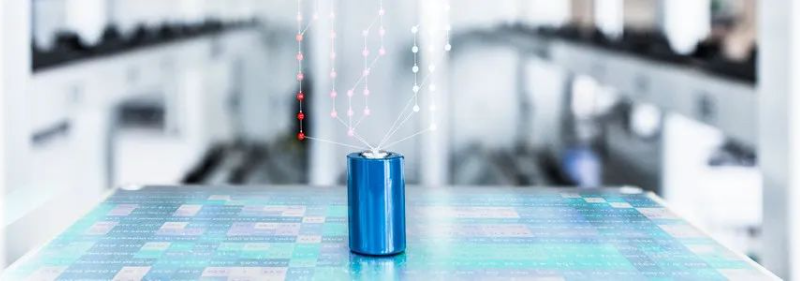
© Fraunhofer IPA
离子电池是一个正在增长的市场。根据管理咨询公司麦肯锡的估计,仅在欧洲,到2040年就需要80家超级工厂来装配电动汽车、公共汽车和卡车。电池单元的生产——对于带有圆柱形电池的汽车,目前每块电池需要7,000到10,000件电池单元——这不仅是能源密集型的生产,更是资源密集型的生产:除了锂之外,这些电池还含有镍、锰钴、石墨、聚合物和电解质。根据《智能电池制造手册》作者估算,为确保40座电池超级工厂运营将需要相当于7座核电站的能源。其中还未考虑到用于开采原料和将其运输到工厂所需的能源。
“为了提高生产效率和可持续性,必须优化电池生产过程。”斯图加特大学电能存储系统负责人兼Fraunhofer IPA数字化电池生产中心负责人以及本册的作者Kai Peter Birke教授解释说。如今的电池生产加工水平仍与 1960 年代汽车行业的水平大致相同:尝试一下,看看它们是否在实践中有效,然后调整制造工艺。这种试错法不仅效率很低,而且很繁琐,也会消耗能源和资源。
© Fraunhofer IPA
作者团队坚信,电池的资源节约和节能生产的关键在于数字化。数字化生产控制不仅可以加快制造过程,灵活适应客户要求,还可以及早发现质量缺陷:可以对不符合标准的组件进行分类,数字化错误分析还可以迅速查明质量差的产品原因,还可以重新调整制造工艺。这样可以节省时间、材料和能源。
Birke解释说:“可以使用在生产过程中收集的数据为每个电池创建一个配置文件,该配置文件在整个产品生命周期中都伴随着它。”例如,这样的配置文件将包含有关构成电池的材料的信息。确定电极由什么物质制成以及添加了多少电解质 - Fraunhofer IPA专门为此开发了一种智能工件载体,例如,它可以数字化方式确定重量。
事实上,这种可以通过电池表面上的二维码调用的数字配置文件将有助于更有效地使用它,Birke强调说:“成品电池的使用寿命取决于个体电池单元容量 - 容量差异越小,电池的使用寿命越长。如果电池制造商通过数字配置文件知道每个组电池的容量,他们可以有针对性地选择它们并将它们组装到高质量的电池。,,在运行过程中,配置文件将帮助电池管理系统控制充电过程,以便电池管理系统的信息决定电池的性能,这对于想要挑选出最强大的电池以供二次使用的回收商来说将是有帮助的。其余的可以按类型分解并重新使用。
“对整个生命周期进行如此全面的数字化还有很长的路要走,”Birke 强调说,但是,我们的研究表明,在数字化转型过程中的投资为制造商带来了巨大的回报,因为它们不仅节省了材料和能源成本,而且他们的产品也可以进行改进”。